Enjoy French jams with confidence : the expertise of the quality service of your Andrésy Confitures jam maker !
15
July 2020
How can we guarantee that your high-end jams are produced in complete safety and hygiene ? Learn all about the essential work of the quality service of your jam maker !
With the COVID-19 health crisis we have just gone through and the concerns that persist, your customers and consumers are once again asking questions about hygiene and food safety.
Do you know how your jam maker ensures that everything is in place to produce high-end jams safely? Do you know all the actions that have been taken or reinforced to deal with the risks of the COVID-19 virus?
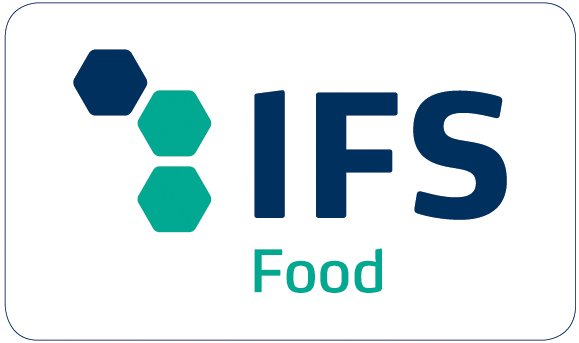
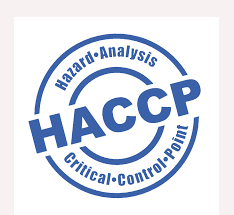
What is the role of the quality service at your jam producer ?
At Andrésy Confitures, the quality department represents 10% of the total workforce. This is to say its importance!
Do you know what a quality service for a jam maker is for? The quality department ensures that all hygiene, food safety and traceability procedures are respected.
These procedures are listed in several filing cabinets which group together the documents, procedures and actions followed by your jam maker.
They often follow 2 standards in France : HACCP system and more recently IFS FOOD. The quality department also carries out regulatory and health monitoring and ensures that the company, its teams and its products are always up to date with new regulations.
The quality team of Andrésy Confitures has mastered these standards for years and the jam maker proudly displays the certifications results of its work.
As proof, 100% of quality audits have been successfully passed !
At the Ile de France jam workshop, all the people who produce your premium jams are trained each year in quality, safety and hygiene rules.
For the production of quality French jams, hygiene gestures and safety and traceability monitoring are observed throughout the year thanks to the actions of the quality department : regulatory watch, training, formalization of rules and controls, daily monitoring of people and productions, etc.

What special measures were taken by your jam maker from the start of COVID-19 and during the crisis?
From March, the quality department of your jam maker applied a crisis management procedure :
– opening of a logbook for daily monitoring
– daily inventory of changes in government decrees linked to the virus
– Establishment of a crisis management unit made up of management and quality manager, Josiane Brauchli
– Writing of a letter by Mrs. Brauchli to inform customers, suppliers and service providers of the procedures implemented and adjustments to production
Internally also, actions have been implemented to maintain the production of your high-end jams while respecting the health of each person :
– individual day-to-day monitoring
– Training in individual self-monitoring protocols
– Communication on hygiene instructions to be respected inside and outside the company
– Elimination of all non-essential meetings and implementation of rules for the removal of essential meetings
All the people who work in the production of your high-end jams at Andrésy Confitures are already used to respecting the strict rules of the IFS throughout the year. This discipline imposed by the French jam maker has enabled rapid and effective adaptation to the additional constraints linked to COVID-19 !
What interactions with customers does Andrésy’s quality service develop?
In normal times, the quality department informs about regulations, verifies the legal compliance of products and packaging, ensures the conformity of productions with customer requirements, provides product sheets and all specific requests.
During the COVID-19 health crisis, the jammer quality team transmitted its crisis management protocol to customers in March to inform and reassure them. He also provided an interface between the actions requested by the internal protocols of certain customers and the production of high-end jams. He consulted suppliers and secured the manufacturing stages: from the orchard to your shops and establishments!
Even today, what actions are continuing ?
Since the beginning of April, the quality service continues to play its full role in a different and yet still as secure context :
– recovery protocol with formalization of mandatory barrier gestures, behavior guidelines in public transport or car-sharing, behavior to adopt in case of symptoms
– Addition of disinfection stations and additional procedures in production and also in break and meal spaces
– Choice of equipment suitable for the production of high-end jams left to everyone: surgical masks or visors, in addition to the usual work clothes, gloves, boots and charlottes
– Modification of workshops to respect social distancing: additions of Plexiglas, shifts in working hours, reception of carriers and service providers, display of distancing diagrams
The daily vigilance of the quality service of your jam maker benefits everyone, in times of crisis as in a more “normal” everyday life.
Health and regulatory monitoring, ongoing training for teams and customers, assistance provided to everyone to adapt to their daily actions, keeping traceability or regulatory documents, are all actions carried out throughout the year by the quality service of Andrésy Confitures and who participate in producing exceptional French jams !
Do you want to know more about the measures taken by your jam maker ?
Coliseurs, what new features can you add to your gourmet gourmet baskets to keep them attractive?
 Accueil  23April 2024Parcels are highly appreciated by companies to honor their customers, by works councils for employees, and more generally by all those who receive them.Of all the different types of parcel, gourmet food baskets are an...
New: Andrésy Bio is now available! New recipes, new design… Why choose an organic jam for your establishment?
 Accueil  16April 2024Did you know that Maison Andrésy was one of the first jam makers to market an organic jam? Long before stores and consumers became aware of the benefits of organic produce, Maison Andrésy created...
Wondering which fruits are best for making jam ? Maison Andrésy, your expert in fruit sourcing, gives you its selection criteria!
 Accueil  6April 2024 In 2021, the Cassan family, who have run Maison Andrésy for 3 generations, decided that the motto of the family jam factory would be: "Sourcing the best of Nature to offer you the excellence of our know-how"....